Beautiful Plants For Your Interior
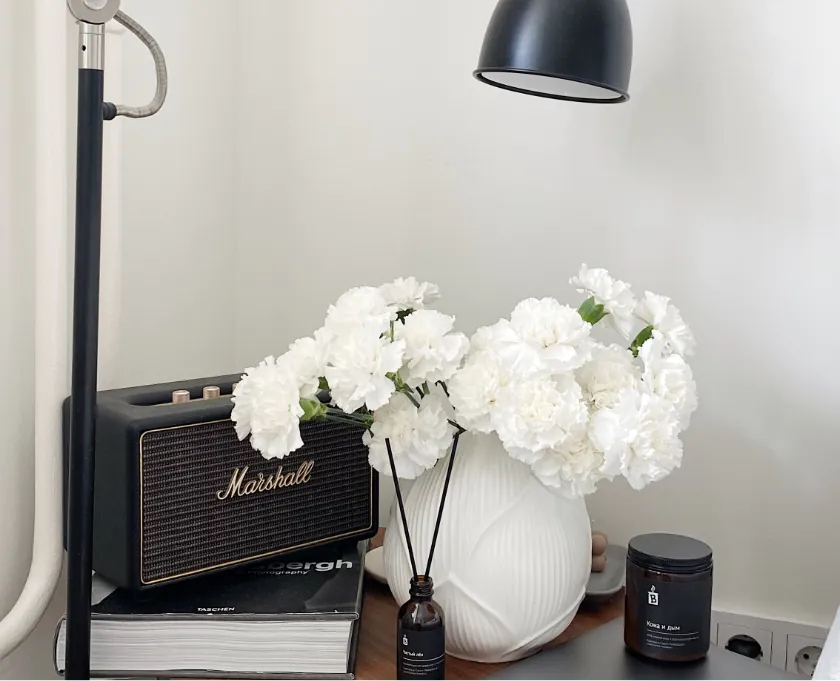
The production of cigar labels (also known as cigar rings or cigar bands) involves material selection, process design, and equipment application, with the core goal of achieving the combination of brand identity, anti counterfeiting function, and aesthetic value. The following are the key elements and processes for producing cigar labels:
1. Material selection
1. Basic materials
Paper: commonly used copperplate paper, coated paper or special paper, suitable for traditional cigar labels, with low cost and strong printability.
Metal foil: such as aluminum foil and copper foil, used for high end cigar labels, giving metal luster and luxurious texture.
Plastic film, such as polyester (PET) or polypropylene (PP), is moisture resistant, wear resistant, and suitable for storing cigars in special environments.
Gracin paper: Used as a substrate for RFID electronic tags, it has flexibility and easy peeling properties to avoid damaging the cigar wrapper.
2. Functional materials
Adhesive: Water based adhesive or hot melt adhesive, which needs to balance viscosity and cigar surface protection to avoid residue or detachment.
Anti counterfeiting technology materials, such as fluorescent ink, temperature change ink, laser holographic film, etc., are used for anti counterfeiting labels.
RFID components: including chips, Dry Inlay (antenna and chip combination layer), used to track the entire cigar production process.
2. Production Process and Steps
1. Design and plate making
Design label patterns based on brand requirements, including brand logo, place of origin, anti counterfeiting code, and other information, and complete layout through professional software.
High end labels may be combined with artistic design, such as hand drawn patterns or relief effects.
2. Printing process
Offset Printing: Suitable for mass production of paper labels with high color reproduction.
Concave printing/screen printing : Used for metal foil or plastic labels to enhance the three dimensional sense and durability of patterns.
Digital Printing: Suitable for small batch customization, with strong flexibility and the ability to quickly adjust designs.
3. Functional layer processing
Application of anti counterfeiting technology: If adding fluorescent coating, laser engraving anti counterfeiting codes or invisible patterns, they need to be completed through specialized equipment after printing.
RFID tag integration : Fix the chip and Dry Inlay layer on the substrate (such as Gracin paper) with glue, ensuring that the tag is only locally glued when wrapped around the cigar to avoid damaging the wrapper.
4. Die cutting and slitting
Use a die cutting machine to cut the printed roll into standard sizes (such as RFID tag size of 30mm × 100mm) or customized shapes (circular, elliptical, etc.).
The slitting equipment is used to cut large rolls of material into small rolls for subsequent packaging.
5. Quality Inspection and Packaging
Check the printing accuracy, adhesion, anti counterfeiting function, and RFID signal stability of the label, and remove defective products.
The packaging forms include roll packaging (convenient for automated labeling) or sheet packaging (used for manual labeling).
3. Key Equipment
1. Printing equipment
Offset printing machines, gravure printing machines, and screen printing machines are used for pattern printing of labels made of different materials.
2. Die cutting machine
CNC die cutting machines achieve high precision cutting and adapt to complex shape requirements.
3. RFID packaging equipment
Used for precise bonding between chips and antennas, ensuring signal stability and tag durability.
4. Coating machine
Apply glue or anti counterfeiting coating to control the thickness and uniformity of the adhesive layer.
5. Automated labeling machine
Suitable for large scale production, improving labeling efficiency and consistency.
4. Special Processes and Technical Difficulties
1. Adhesive viscosity control
It is necessary to balance the adhesion and cleanliness of the label on the surface of the cigar during peeling, in order to avoid residue or damage to the wrapper.
2. Environmental adaptability
Cigar storage environment has high humidity (70% 75%), labels need to be moisture resistant and not fade, and material selection needs to pass strict testing.
3. Anti counterfeiting and traceability
Anti counterfeiting labels need to be combined with multiple technologies (such as QR codes and RFID) to achieve full process traceability, and the complexity of technology integration is high.
V. Application Scenario Expansion
1. High end customization : Handmade cigars are often paired with artistic labels, such as hot stamping and relief techniques, to enhance their collection value.
2. Anti counterfeiting and traceability: RFID tags are used to record the time, place of origin, and circulation information of cigar rolls, meeting the needs of consumers for authenticity verification.
3. Limited edition design : Special events (such as brand anniversaries) will introduce limited edition labels, combined with anti counterfeiting technology to enhance scarcity.
Through the above process, cigar labels not only carry brand image and anti counterfeiting functions, but also become an important symbol of cigar culture. Its production needs to balance aesthetics, functionality, and technical precision to ensure stable performance in complex environments.